Audit énergétique fours de cuisson
Audit énergétique fours de cuisson
Les fours de cuisson industriels, utilisés dans divers secteurs tels que l’industrie alimentaire, la métallurgie et la céramique, sont connus pour leur consommation énergétique élevée. C’est pourquoi un audit énergétique fours de cuisson est essentiel pour identifier les opportunités d’amélioration de l’efficacité énergétique et de réduction des coûts, tout en minimisant l’impact environnemental.
Audit énergétique fours de cuisson : c’est quoi ?
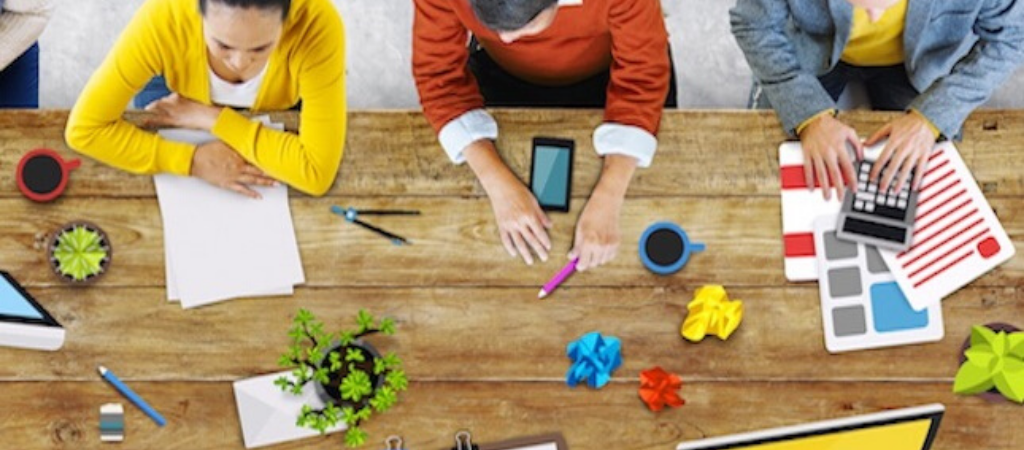
Avant d’aborder l’audit énergétique proprement dit, il est important de comprendre les différents types de fours de cuisson industriels et les défis énergétiques auxquels ils sont confrontés. Les fours de cuisson peuvent fonctionner au gaz, à l’électricité, au charbon ou à d’autres combustibles, et leur efficacité énergétique dépend de plusieurs facteurs tels que l’isolation thermique, la régulation de la température, le système de récupération de chaleur, etc.
L’audit énergétique fours de cuisson est un processus essentiel pour les industries utilisant ces équipements. Il permet d’identifier les opportunités d’amélioration de l’efficacité énergétique, de réduire les coûts énergétiques, de minimiser l’impact environnemental et d’améliorer la productivité. En prenant des mesures pour optimiser l’efficacité énergétique des fours de cuisson, les entreprises peuvent jouer un rôle actif dans la transition vers une économie plus durable et contribuer à la protection de l’environnement.
L’audit énergétique fours de cuisson joue un rôle crucial dans l’amélioration de la performance énergétique des fours de cuisson. Il assure l’évaluation des performances énergétiques actuelles des fours de cuisson. Cela inclut l’analyse de la consommation d’énergie, des processus de cuisson, des schémas de fonctionnement, des pertes de chaleur, etc. L’évaluation initiale fournit une compréhension approfondie des inefficacités et des opportunités d’amélioration. Il permet également d’identifier les opportunités d’amélioration en se basant sur les résultats de l’évaluation. Cela peut inclure des mesures telles que l’optimisation des cycles de cuisson, l’isolation thermique, l’installation de dispositifs de récupération de chaleur, l’amélioration des systèmes de contrôle, etc.
L’audit énergétique fours de cuisson effectue une analyse coûts-bénéfices pour évaluer la viabilité économique des mesures d’amélioration proposées. Cela permet de déterminer les investissements nécessaires, les économies d’énergie potentielles, les périodes de retour sur investissement et les bénéfices financiers attendus. Cette analyse aide les entreprises à prendre des décisions éclairées concernant les mesures à mettre en œuvre.
Ensuite, l’audit énergétique fournit un plan d’action détaillé pour mettre en œuvre les mesures d’amélioration identifiées. Le plan d’action décrit les étapes spécifiques à suivre, les ressources requises, les responsabilités, les échéances et les indicateurs de suivi. Cela permet une mise en œuvre cohérente et efficace des mesures d’amélioration. L’audit énergétique fours de cuisson inclut également des mécanismes de suivi et d’évaluation pour mesurer les progrès réalisés et évaluer l’efficacité des mesures d’amélioration mises en place. Cela peut impliquer la collecte de données de consommation d’énergie, l’analyse des performances, la comparaison avec les objectifs fixés, etc. Le suivi régulier permet d’identifier les problèmes potentiels et d’apporter des ajustements si nécessaire.
En utilisant l’audit énergétique fours de cuisson comme outil, les entreprises peuvent améliorer la performance énergétique de leurs fours de cuisson en identifiant les domaines d’amélioration, en prenant des mesures ciblées et en surveillant les progrès réalisés. Cela conduit à des économies d’énergie, à une réduction des coûts opérationnels, à une diminution de l’empreinte environnementale et à une meilleure durabilité globale du processus de cuisson.
Les étapes de l’audit énergétique fours de cuisson
La première étape de l’audit énergétique fours de cuisson consiste à collecter des données précises sur les fours de cuisson, y compris les caractéristiques techniques, les cycles de fonctionnement, les consommations énergétiques, etc. Ces données serviront de base pour l’analyse approfondie ultérieure.
À l’aide des données collectées, l’auditeur énergétique peut effectuer une analyse détaillée pour évaluer l’efficacité énergétique des fours de cuisson. Cela peut inclure l’examen des performances thermiques, l’identification des pertes énergétiques, l’évaluation de l’utilisation des ressources, etc.
Sur la base des résultats de l’analyse, des possibilités d’amélioration de l’efficacité énergétique peuvent être identifiées. Cela peut inclure des recommandations telles que l’isolation thermique renforcée, l’optimisation des cycles de fonctionnement, l’utilisation de technologies de récupération de chaleur, etc.
Avant de mettre en œuvre les recommandations, une analyse coûts-bénéfices est essentielle pour évaluer la viabilité économique des mesures proposées. Cela permettra de déterminer le retour sur investissement potentiel et de prioriser les actions à entreprendre.
Une fois l’analyse coûts-bénéfices terminée et les mesures d’amélioration identifiées, il est temps de passer à la mise en œuvre. Cela peut inclure la réparation ou le remplacement des équipements défectueux, l’installation de dispositifs d’isolation thermique, l’optimisation des procédures de fonctionnement, l’intégration de systèmes de récupération de chaleur, etc. Il est recommandé de suivre un plan d’action détaillé et de veiller à ce que les mesures soient mises en œuvre de manière efficace et cohérente.
Enfin, il est important de surveiller régulièrement les performances énergétiques des fours de cuisson. Cela permet de s’assurer que les objectifs d’efficacité énergétique sont atteints et d’apporter d’éventuelles corrections si nécessaire. Un suivi régulier aidera également à évaluer l’impact des mesures prises et à identifier de nouvelles opportunités d’amélioration.
Pourquoi faire un audit énergétique fours de cuisson
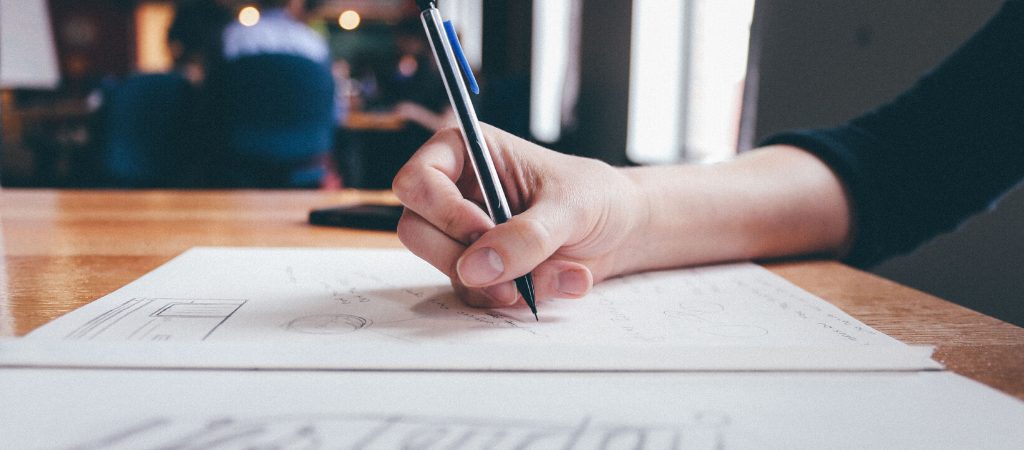
L’audit énergétique fours de cuisson présente un ensemble d’avantage pour l’entreprise auditée, à savoir :
- Réduction des Coûts Énergétiques
L’audit énergétique fours de cuisson permet d’identifier les sources de gaspillage énergétique et de proposer des mesures d’amélioration ciblées. En optimisant l’efficacité énergétique des fours de cuisson, les entreprises peuvent réduire significativement leurs coûts énergétiques, ce qui se traduit par des économies financières à long terme.
- Réduction de l’Impact Environnemental
En améliorant l’efficacité énergétique des fours de cuisson, les émissions de gaz à effet de serre et la consommation de ressources naturelles peuvent être réduites. Cela contribue à la lutte contre le changement climatique et à la préservation de l’environnement.
- Amélioration de la Productivité
Des fours de cuisson plus efficaces peuvent conduire à une meilleure productivité, grâce à des cycles de cuisson optimisés, des temps de préchauffage réduits et une meilleure régulation de la température. Cela permet d’augmenter la capacité de production tout en maintenant la qualité des produits.
- Conformité aux Réglementations
Dans de nombreux pays, il existe des réglementations strictes en matière d’efficacité énergétique et d’émissions de gaz à effet de serre. En réalisant un audit énergétique des fours de cuisson, les entreprises peuvent s’assurer de respecter ces réglementations et éviter les sanctions potentielles.
Audit énergétique fours de cuisson : impact environnemental des fours de cuisson industriels
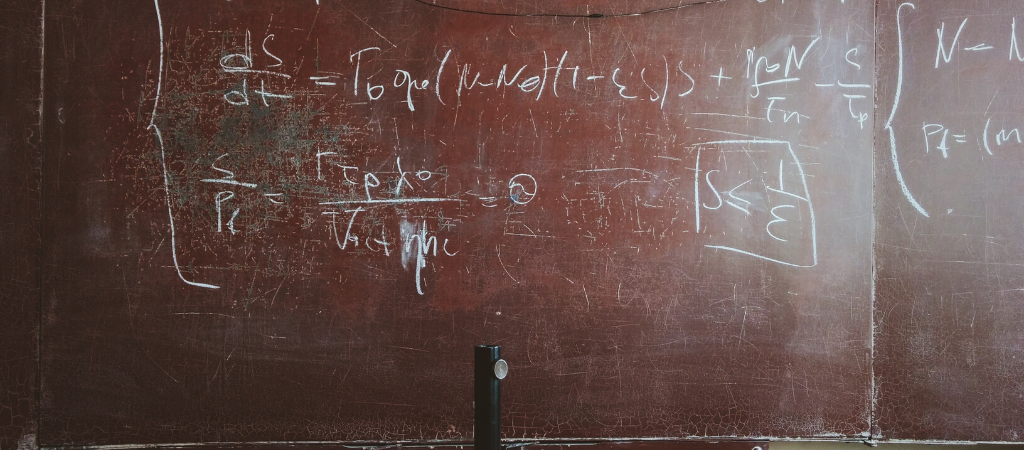
Les fours de cuisson industriels ont un impact significatif sur l’environnement en raison de leur consommation énergétique élevée et de leurs émissions de gaz à effet de serre. Les fours de cuissons industriels impactent l’environnement de ces manières :
- Les fours de cuisson utilisent souvent des combustibles fossiles tels que le gaz naturel, le charbon ou le fioul pour générer la chaleur nécessaire au processus de cuisson. La combustion de ces combustibles fossiles libère du dioxyde de carbone (CO2) et d’autres gaz à effet de serre dans l’atmosphère, contribuant ainsi au changement climatique et à l’augmentation de l’effet de serre.
- Les fours de cuisson industriels nécessitent une quantité considérable d’énergie pour atteindre et maintenir les températures de cuisson requises. Cette demande énergétique élevée entraîne une consommation importante de ressources énergétiques, qu’elles proviennent de sources renouvelables ou non. L’utilisation intensive d’énergie non renouvelable a un impact sur la disponibilité des ressources et sur l’empreinte écologique globale.
- Outre les émissions de gaz à effet de serre, les fours de cuisson peuvent également produire des polluants atmosphériques tels que les oxydes d’azote (NOx), les particules fines, les composés organiques volatils (COV) et le monoxyde de carbone (CO). Ces polluants peuvent avoir des effets néfastes sur la qualité de l’air, la santé humaine et contribuer à la formation de smog et de problèmes respiratoires.
- Certains processus de cuisson industrielle génèrent des déchets solides ou liquides, tels que les résidus de combustion, les cendres, les boues ou les effluents. Une gestion inadéquate de ces déchets peut entraîner des problèmes de contamination des sols, des eaux souterraines et des écosystèmes environnants.
- Les fours de cuisson industriels nécessitent l’utilisation de matériaux réfractaires, tels que la brique réfractaire, pour résister aux températures élevées. L’extraction et la production de ces matériaux peuvent avoir un impact sur les ressources naturelles, y compris l’épuisement des ressources non renouvelables et la dégradation des écosystèmes associés à l’extraction minière.
La combinaison de ces impacts environnementaux souligne l’importance de mettre en œuvre des pratiques d’efficacité énergétique et des technologies propres pour réduire l’empreinte environnementale des fours de cuisson industriels. L’audit énergétique fours de cuisson peut jouer un rôle clé dans l’identification des opportunités d’amélioration et la mise en place de mesures visant à réduire ces impacts.
Audit énergétique fours de cuisson : Les types de fours de cuisson industriels
Il existe différents types de fours de cuisson industriels, adaptés à des applications spécifiques dans divers secteurs industriels. Voici certains des types de fours de cuisson industriels les plus courants :
- Fours à convection : Les fours à convection sont largement utilisés dans l’industrie alimentaire, tels que les boulangeries, les pâtisseries et les restaurants. Ils utilisent des ventilateurs pour faire circuler l’air chaud à l’intérieur du four, assurant une répartition uniforme de la chaleur. Ces fours sont idéaux pour la cuisson de produits tels que les pains, les pâtisseries et les pizzas.
- Fours à infrarouge : Les fours à infrarouge utilisent des radiations infrarouges pour chauffer les aliments ou les matériaux à cuire. Ils sont utilisés pour la cuisson rapide, telle que la cuisson de pizzas surgelées, de produits de boulangerie ou de viandes. Les fours à infrarouge offrent des temps de cuisson plus courts et une meilleure efficacité énergétique par rapport aux autres types de fours.
- Fours à sole rotative : Ces fours sont couramment utilisés dans l’industrie de la boulangerie et de la pâtisserie. Ils se composent d’une sole rotative sur laquelle les produits sont placés pour la cuisson. Les fours à sole rotative permettent une cuisson uniforme et contrôlée des produits, avec la possibilité de régler la vitesse de rotation et les paramètres de cuisson.
- Fours à tunnel : Les fours à tunnel sont utilisés dans l’industrie alimentaire pour la cuisson en continu de produits tels que les biscuits, les snacks, les viennoiseries, etc. Ils se composent d’un tunnel de cuisson à travers lequel les produits sont transportés sur des bandes transporteuses. Ces fours offrent une grande capacité de production et permettent un contrôle précis de la température et du temps de cuisson.
- Fours à gaz ou à charbon : Ces fours sont utilisés dans diverses industries, y compris la métallurgie, la céramique et la verrerie. Ils utilisent du gaz naturel ou du charbon comme combustible pour générer la chaleur nécessaire à la cuisson des matériaux. Ces fours peuvent atteindre des températures très élevées et sont adaptés aux processus de fusion, de traitement thermique et de cuisson de matériaux spécifiques.
- Fours de séchage : Les fours de séchage sont utilisés pour éliminer l’humidité des matériaux, tels que les produits chimiques, les textiles, les céramiques, etc. Ils sont conçus pour fournir une chaleur douce et uniforme pour évaporer l’humidité sans endommager les matériaux.
A PROPOS de NPM
« Le Cabinet New Performance Management est le fruit d’une longue expérience professionnelle au sein de grands groupes Internationaux, d’un profond attachement aux valeurs de travail en entreprise, d’amitié et de performance.
Nous conseillons et accompagnons les entreprises et les particuliers dans leur développement et mettons quotidiennement en œuvre des moyens humains et un savoir-faire à la hauteur des ambitions de nos clients.
Notre approche ciblée et qualitative nous permet de bénéficier d’une place de premier plan dans certains domaines comme l’ingénierie de la sécurité incendie, les études Environnementales, le conseil QSE, le Coaching, l’intelligence relationnelle au sein des équipes et la formation continue et certifiante.
New Performance Management, c’est avant tout un savoir-faire et un esprit d’équipe dont les enjeux sont la satisfaction de nos clients et l’épanouissement professionnel des équipes au Travail.
Notre valeur ajoutée : « un challenge au quotidien, des liens de confiance solides, un service sur mesure et l’utilisation des derniers outils du conseil pour des processus que nous souhaitons toujours plus performant. ».
consultants et formateurs expérimentés
Nos consultants et nos formateurs sont tous certifiés et sont des ingénieurs de Grandes Ecoles, avec plus de 16 d’expériences professionnelles dans des multinationales et des PME.