FORMATION AMDEC
FORMATION AMDEC AU MAROC
La mise en place de produits et systèmes de plus en plus complexes et performants conduisent les entreprises à mettre en œuvre des méthodes de prévention rigoureuses tant au niveau de la conception des produits que de la mise en œuvre de nouveaux processus, à l’image de la formation AMDEC.
La formation AMDEC au Maroc permet à un responsable ou animateur qualité ou de développement de comprendre, mettre en œuvre et animer la méthode AMDEC. Les objectifs de la formation AMDEC au Maroc sont :
- Apprendre à piloter et animer un groupe de travail AMDEC.
- Acquérir une connaissance méthodologique et pratique approfondie de l’AMDEC (Analyse des modes de défaillance, de leurs effets et de leur criticité) dans ses différentes composantes (produit, procédé, moyen de production, processus),
1.Formation AMDEC: AMDEC, qu’est-ce que c’est ?
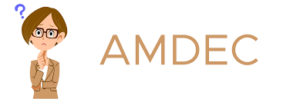
L’AMDEC, Analyse des Modes de Défaillances, de Leurs Effets et de leur Criticité (ou FMEA : Failure Mode and Effects Analysis) est une méthode rigoureuse et préventive visant à recenser les défaillances potentielles d’un système et/ou d’un élément. Il faut définir des actions pour éliminer ces défaillances, réduire leurs effets et détecter et empêcher les causes. Cette méthode permet de structurer le processus du développement. L’AMDEC est un outil qui consiste à prévoir pour ne pas être obligé de revoir. Il existe plusieurs sortes d’AMDEC : l’AMDEC du concept, produit, procédé, moyen, de la machine, …
Toutes ont la même structure et suivent les mêmes étapes. C’est un outil indispensable pour la maîtrise de la qualité et de la sécurité . La méthode AMDEC est très utilisée dans le secteur de l’automobile, de l’aéronautique et du ferroviaire. Une méthode dérivée de l’AMDEC est utilisée dans l’agroalimentaire, la chimie et le secteur pharmaceutique : le HACCP
L’AMDEC est une technique d’analyse prévisionnelle qui permet d’estimer les risques d’apparition de défaillance ainsi que les conséquences sur le bon fonctionnement du moyen de production, et d’engager les actions correctives nécessaires. L’objectif principal est l’obtention d’une disponibilité maximale. Les objectifs intermédiaires sont les suivants :
- Analyser les conséquences des défaillances,
- Identifier les modes de défaillances,
- Préciser pour chaque mode de défaillance les moyens et les procédures de détection,
- Déterminer l’importance ou la criticité de chaque mode de défaillance,
- Classer les modes de défaillance,
- Etablir des échelles de signification et de probabilité de défaillance.
2.Formation AMDEC : Les types d’AMDEC
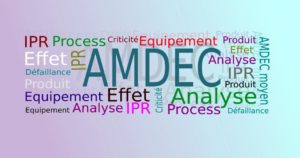
Il existe globalement Cinq types d’AMDEC suivant le système analysé :
- AMDEC-Produit: L’AMDEC-Produit est utilisée pour l’aide à la validation des études de définition d’un nouveau produit fabriqué par l’entreprise. Elle est mise en œuvre pour évaluer les défauts potentiels du nouveau produit et leurs causes. Cette évaluation de tous les défauts possibles permettra d’y remédier, après hiérarchisation, par la mise en place d’actions correctives sur la conception et préventives sur l’industrialisation
- AMDEC-Process : L’AMDEC-Process est utilisée pour étudier les défauts potentiels d’un produit nouveau ou non, engendrés par le processus de fabrication. Elle est mise en œuvre pour évaluer et hiérarchiser les défauts potentiels d’un produit dont les causes proviennent de son processus de fabrication. S’il s’agit d’un nouveau procédé, l’AMDEC-Process en permettra l’optimisation, en visant la suppression des causes de défaut pouvant agir négativement sur le produit. S’Il s’agit d’un procédé existant, l’AMDEC-Process en permettra l’amélioration.
- AMDEC- Moyen de production : L’AMDEC – Moyen de production, plus souvent appelée AMDEC-Moyen, permet de réaliser l’étude du moyen de production lors de sa conception ou pendant sa phase d’exploitation. À la conception du moyen de production, la réalisation d’une AMDEC permet de faire le recensement et l’analyse des risques potentiels de défaillance qui auraient pour conséquence d’altérer la performance globale du dispositif de production, l’altération de performance pouvant se mesurer par une disponibilité faible du moyen de production. Dans ce cas de figure, l’analyse est conduite sur la base des plans et/ou prototypes du moyen de production.
- AMDEC Fonctionnel : Permet, à partir de l’analyse fonctionnelle (conception), de déterminer les modes de défaillances ou causes amenant à un événement redouté.
- AMDEC Flux : Permet d’anticiper les risques liés aux ruptures de flux matière ou d’informations, les délais de réaction ou de correction, les coûts inhérents au retour à la normale.
3.Formation AMDEC: Démarche pratique de l’AMDEC
L’emploi des AMDEC crée une ossature qu’il convient de compléter et d’outiller. Pour cela une analyse plus fine de la pertinence des informations est nécessaire. Le groupe AMDEC est tenu de maîtriser la machine et de mettre à jour et s’assurer de la validité de toutes les informations utiles à l’étude. Il appartient à ce groupe de s’appuyer sur le retour d’expérience de tous les opérateurs de tous les services du cycle de fabrication du produit, qui peuvent apporter une valeur ajoutée à l’analyse.
La démarche pratique de l’AMDEC se décompose en 4 étapes suivantes :
- Etape 1 : initialisation de l’étude qui consiste :
- La définition de la machine à analyser,
- La définition de la phase de fonctionnement,
- La définition des objectifs à atteindre,
- La constitution du groupe de travail,
- La définition du planning des réunions,
- La mise au point des supports de travail.
- Etape 2 : description fonctionnelle de la machine qui consiste :
- Découpage de la machine,
- Inventaire des fonctions de service,
- Inventaire des fonctions techniques.
- Etape 3 : analyse AMDEC qui consiste :
- Analyse des mécanismes de défaillances,
- Evaluation de la criticité à travers : la probabilité d’occurrence F, la gravité des conséquences : G, la probabilité de non détection D. (La criticité est définie par le produit : C=F.G. D)
- Propositions d’actions correctives.
- Etape 4 : synthèse de l ’étude/décisions qui consiste :
- Bilan des travaux,
- Décision des actions à engager.
- Etape 5 : Suivre
- Analyser les solutions correctives proposées jusqu’à ce que les IPR soient inférieurs aux seuils. „
- Etape 6 : Appliquer
- Les solutions correctives, validées lors du suivi, sont appliquées ;
- Étape très importante car on corrige effectivement les défaillances potentielles.
- Etape 7 : Vérifier
- Vérifier l’efficacité des mesures prises sur le terrain ;
- Capitaliser l’expérience en archivant l’étude dans une base de données.
A PROPOS de NPM
« Le Cabinet New Performance Management est le fruit d’une longue expérience professionnelle au sein de grands groupes Internationaux, d’un profond attachement aux valeurs de travail en entreprise, d’amitié et de performance.
Nous conseillons et accompagnons les entreprises et les particuliers dans leur développement et mettons quotidiennement en œuvre des moyens humains et un savoir-faire à la hauteur des ambitions de nos clients.
Notre approche ciblée et qualitative nous permet de bénéficier d’une place de premier plan dans certains domaines comme l’ingénierie de la sécurité incendie, les études Environnementales, le conseil QSE, le Coaching, l’intelligence relationnelle au sein des équipes et la formation continue et certifiante.
New Performance Management, c’est avant tout un savoir-faire et un esprit d’équipe dont les enjeux sont la satisfaction de nos clients et l’épanouissement professionnel des équipes au Travail.
Notre valeur ajoutée : « un challenge au quotidien, des liens de confiance solides, un service sur mesure et l’utilisation des derniers outils du conseil pour des processus que nous souhaitons toujours plus performant. ».
consultants et formateurs expérimentés
Nos consultants et nos formateurs sont tous certifiés et sont des ingénieurs de Grandes Ecoles, avec plus de 16 d’expériences professionnelles dans des multinationales et des PME.